Bluelite was delighted to be named winner of the Sustainable/Ethical Manufacturer Award at the Insider Media ‘Made in the South East’ Awards. It’s a shared endeavour for all our people, both in work and at home. Here’s some of our progress so far.
Bluelite’s commitment to minimising our carbon footprint and reducing our environmental impact is central to our sustainability journey.
For example, our investment in 88 solar panels has reduced our reliance on fossil fuel generated electricity by 10%, with half of our power requirements now met through renewables.
We are adopting a more sustainable approach across our production process, including the use of low solvent inks, LED lighting throughout and electric vehicles for service support.
Our waste management practices include cardboard recycling for packing kits and the complete elimination of bubble wrap. We vacuum seal packages to minimise materials usages and tapes, have replaced single use plastic cups with china cups and also share materials offcuts with local schools to provide high visibility markings for bags and satchels. Office operations are now largely paperless, with all records stored digitally. Overall, we have reduced waste by 36%, with zero waste sent to landfill.
We also ensure that we incorporate management practices that motivate and involve employees in implementing sustainability measures. We’re also working closely with materials providers to explore ways of making livery application better for the environment in the future.
And to make sure we continue our journey, we are not only accredited to ISO14001, we also use independent assessors to chart our progress on our sustainability journey and challenge us all to do better.
Our Scorecard:
- Carbon footprint: We generate 24,000 kWh of solar power, reducing our carbon emissions by 14,000 kg – which is like planting 650 trees.
- Lower carbon technologies: We invest in lower carbon and more sustainable technologies for day-to-day operations, for example using low solvent inks, LED lighting, and electric vehicles for service support
- Waste reduction: We regularly review processes to minimise waste, prevent waste going to landfill, and reuse resources wherever possible
- We have eliminated single use plastics linked to operational processes, including bubble wrap
- We use backing sheets from materials for wrapping
- We shred cardboard within the factory and reuse it for packaging, thereby eliminating fluted plastic
- We send applicable waste matter to a biomass energy plant
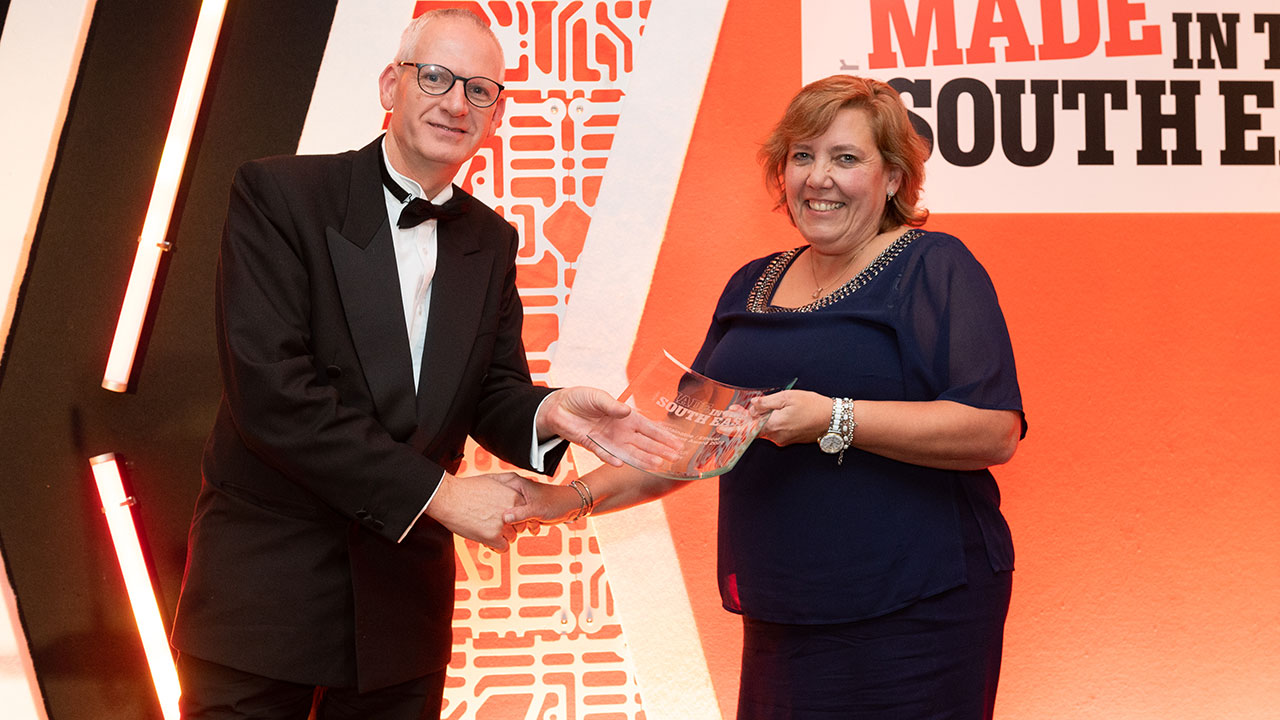